Understanding How Dry Screw Vacuum Pumps Help in Making Semiconductor Chips
Semiconductors are a big part of modern technology. They power our smartphones, computers, the internet, and social media.
New advancements like big data and artificial intelligence are also pushing the semiconductor industry forward. Creating semiconductor chips relies heavily on using vacuum technology throughout various manufacturing stages.
Here’s an in-depth look at how vacuum technology, especially dry screw vacuum pumps, is essential in making semiconductor chips.
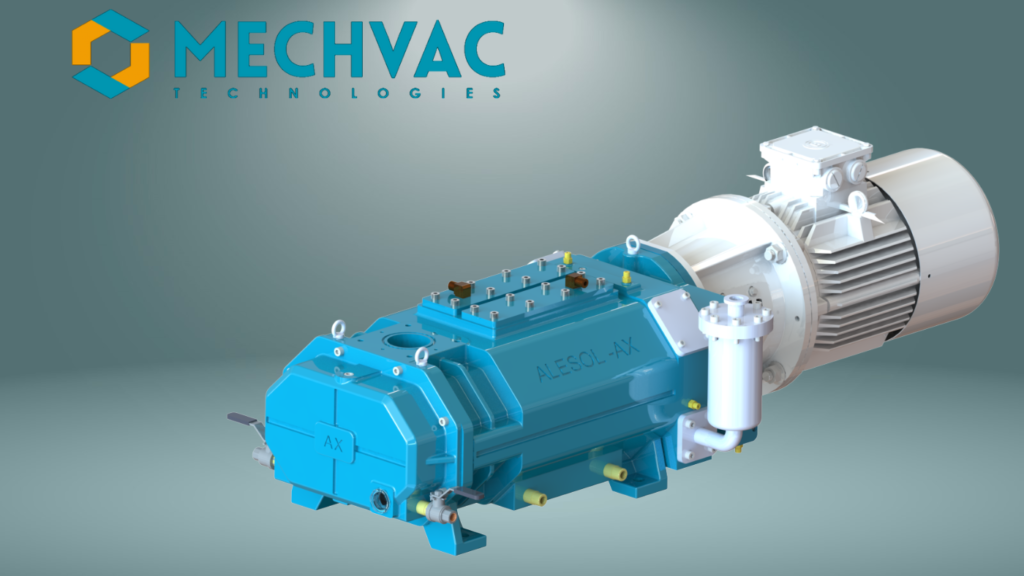
Key Processes in Semiconductor Chip Manufacturing
The semiconductor industry involves many processes, each requiring a unique vacuum level to achieve high-quality results. Here are the main processes involved:
- Deposition
- Etching and Cleaning
- Ion Implantation
- Wafer Handling
- Lithography
- Wafer Inspection and Metrology
Deposition Process
In deposition, layers of insulating and conductive materials are applied to create semiconductor devices. Each layer forms a part of the final chip structure. Various types of deposition techniques are used, including:
- Physical Vapor Deposition (PVD) – Uses plasma-generated ions to coat materials. The PVD process is most effective when paired with dry pumps and turbo or cryo pumps.
- Plasma Enhanced Chemical Vapor Deposition (PECVD) and Atomic Layer Deposition (ALD) – These methods apply critical insulating layers. They operate under primary vacuum in the mbar range.
- Low-Pressure Chemical Vapor Deposition (LPCVD) – This method is used to form thin films and protective layers on the wafer surface.
- Atomic Layer Deposition (ALD) – Works under low vacuum, between 0.1 to 5 mbar, to ensure efficient and fast production rates.
The deposition process is where the chip’s structure begins, setting the foundation for the next stages.
Etching and Cleaning Process
Etching removes specific areas of material to create patterns and structures on the wafer. Cleaning happens between manufacturing steps to prepare the wafer for the next stages and prevent defects. Key points include:
- Dry Dielectric and Polysilicon Etching – Removes small layers, using high-capacity dry pumps in a vacuum of 0.01 to 0.001 mbar.
- Atomic Layer Etching (ALE) – Allows precise removal of a few atomic layers for more detailed chip patterns.
Dry vacuum pumps are critical here as they can work quickly to support high production speeds.
Ion Implantation Process
Ion implantation changes the electrical properties of the wafer by introducing ions into the silicon surface. This stage requires:
- Ion Sources, Beamlines, and End Stations – Each part requires vacuum systems to maintain a clean environment. Turbopumps work alongside dry vacuum pumps for high-quality results.
Good vacuum control ensures no leaks and supports a smooth, uninterrupted process.
Wafer Handling Process
Handling wafers is delicate and needs a vacuum environment to keep the wafer surface clean from any dust particles.
- Vacuum Levels for Load Lock and Transfer Chambers – A fast vacuum setup, combining a turbo and dry vacuum pump, is necessary to keep things efficient.
Lithography Process
Lithography prints patterns onto each layer of the wafer, a critical step in creating detailed circuits. New lithography methods, like Deep Ultra Violet (DUV) and Extreme UltraViolet (EUV), help achieve smaller chip sizes and finer details. EUV uses hydrogen to prevent tin from building up in the equipment. Here, dry vacuum pumps with high hydrogen-handling capabilities are important.
Wafer Inspection and Metrology
Inspection is a quality check stage. Monitoring the process and ensuring accuracy is essential for high-quality chips.
- Low-Vacuum Environments – This stage uses low vacuum to keep the chip clean while measuring each layer.
Important Points to Remember in Semiconductor Manufacturing
- Leak Prevention – A single leak can reduce productivity and affect chip quality.
- Maintenance of Dry Pumps – Regular cleaning and checking of the vacuum system components, like pipes and pumps, ensure long-lasting performance.
About Mechvac Dry Screw (Superscrew) Vacuum Pumps
India’s First Dry Screw Vacuum Pump Manufacturer
Mechvac Vacuum is India’s first company to make dry screw vacuum pumps locally. We have three patents on our GenII Dry Screw Vacuum Pumps, covering design, screw profile, and balancing features.
These pumps are well-suited for challenging applications and can handle corrosive vapors, making them ideal for semiconductor manufacturing.
Why Choose Mechvac Vacuum Pumps?
- Energy-Efficient Design – Our advanced screw design uses less energy than traditional pumps and produces less heat during compression.
- Clean, Oil-Free Operation – Our pumps keep vapors clean and avoid contamination, ideal for environments needing pure vacuum systems.
- Environmentally Friendly – Without oil or water touching the vapors, our pumps create a cleaner, greener manufacturing process.
- Vapor Recovery – Process vapors can be safely released and collected, thanks to the pump’s built-in vent condenser.
Applications Beyond Semiconductors
Our pumps are also used across various industries, such as:
- Chemical and Pharmaceuticals
- Food Processing
- Plastics and Film Evaporation
- Solar PV Manufacturing
Mechvac Technologies PVT LTD are dependable, uniquely designed, and offer high-quality performance, meeting the needs of industries that demand clean, efficient vacuum systems.