Rotary vane vacuum pumps are widely used across industries for creating and maintaining a vacuum, essential in many applications.
Here, we’ll break down different types of vacuum pumps, key considerations for choosing a pump, and the benefits of rotary vane vacuum pumps, along with a comparison to other vacuum technologies.
Let’s also explore how rotary vane pumps are used in different fields and how to maintain them for the best performance.
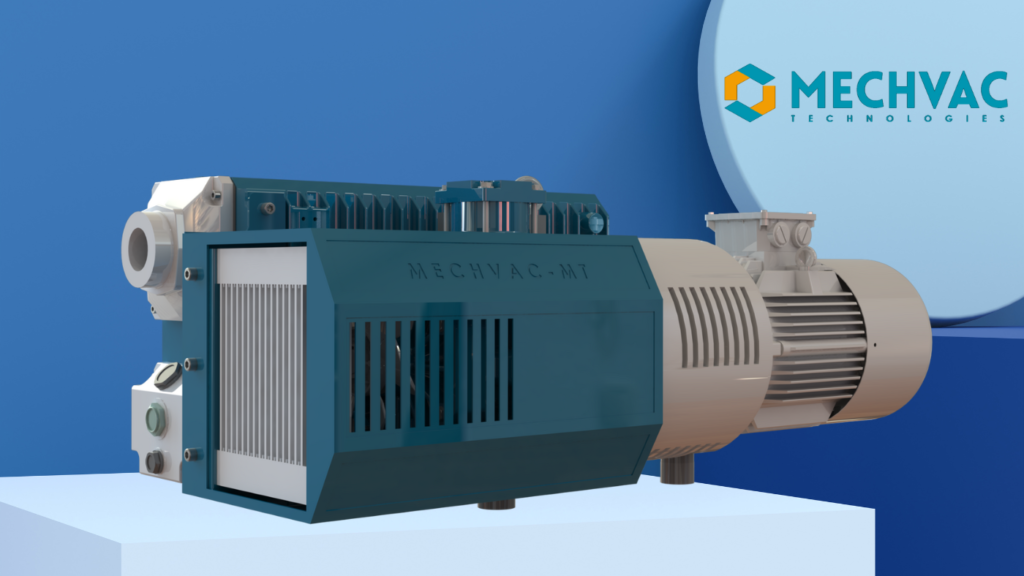
Types of Vacuum Pumps: Choosing the Right Technology
1. Rotary Vane Vacuum Pumps:
These pumps are highly popular due to their reliable performance and compact design. With a rotor and vanes that spin to create a vacuum, rotary vane pumps are efficient, providing a high vacuum level that suits numerous applications.
2. Liquid Ring Vacuum Pumps:
This type of pump uses a liquid (usually water) to generate a seal and create a vacuum. They are ideal for applications involving liquids or high-vapor gases, but they achieve a slightly lower vacuum level than rotary vane pumps.
3. Claw Vacuum Pumps:
Using claw-shaped rotors that spin in opposite directions, these pumps create a clean, oil-free vacuum. They’re ideal for applications that require a contamination-free environment, though they can have a higher upfront cost.
4. Capture or Entrapment Pumps:
These pumps use physical or chemical methods to trap particles and create a vacuum, making them suitable for very high vacuum levels needed in sectors like semiconductor manufacturing.
Key Factors to Consider When Choosing a Vacuum Pump
- Required Vacuum Level: Determine the vacuum level necessary for your application to select a pump that can meet these requirements.
- Flow Rate: Check the volume of gas the pump can move per unit of time, especially if your processes require high throughput.
- Maintenance and Operating Costs: Factor in the cost and frequency of maintenance, including consumables like oil or water.
- Application Specifics and Medium: Some pumps may not work well with certain substances, like flammable or corrosive gases. Choose a pump that suits the type of medium involved.
Rotary Vane Vacuum Pumps: Pros and Cons
Advantages of Rotary Vane Pumps:
- High Vacuum Level: Ideal for a variety of uses due to their efficient vacuum performance.
- Compact and Lightweight: Easy to install and transport, fitting well in space-limited setups.
- Quiet Operation: Low noise and vibration levels make them suitable for quieter environments.
- Cost-Effective: Generally more affordable compared to some other vacuum technologies.
Disadvantages of Rotary Vane Pumps:
- Requires Oil for Operation: Oil lubrication is necessary, which requires regular monitoring and replacement.
- Risk of Oil Contamination: In certain industries (e.g., food or medical), oil leakage may contaminate products.
- Not Suitable for Some Gases: These pumps aren’t ideal for flammable, high-oxygen, or corrosive gases.
Comparing Rotary Vane Vacuum Pumps with Other Technologies
- Liquid Ring Vacuum Pumps: These handle liquids and high-vapor gases well, though they achieve a lower vacuum level than rotary vane pumps. They are often preferred in wet environments.
- Claw Vacuum Pumps: Offering a higher vacuum level than liquid ring pumps, claw pumps are oil-free and suited for clean environments. However, they may have a higher initial cost.
- Capture or Entrapment Pumps: Best for ultra-high vacuum needs, these are typically used in specialized applications, such as in labs or semiconductor production.
Applications of Rotary Vane Vacuum Pumps Across Industries
Automotive Industry:
Used in systems like power brake boosters and emissions control, rotary vane pumps help improve efficiency in various automotive systems.
Laboratories:
These pumps are commonly used in experiments involving vacuum drying, filtration, and distillation, where precise vacuum levels are necessary.
Plastics Industry:
Rotary vane pumps remove moisture during plastic extrusion and create the vacuum needed for shaping in vacuum forming.
Food Packaging Industry:
Vacuum packaging machines rely on rotary vane pumps to remove air, which preserves freshness and extends the shelf life of food products.
Maintenance Tips for Rotary Vane Vacuum Pumps
1. Monitoring Oil Levels:
Check oil levels regularly to ensure the pump functions optimally. Low oil can lead to increased wear and decreased performance.
2. Regular Oil Changes and Filter Replacements:
Follow the manufacturer’s guidelines for oil and filter replacement to maintain efficiency.
3. Troubleshooting Common Issues:
Keep an eye out for issues like oil leaks or unusual noise. Address these promptly to avoid further damage.
Conclusion: How Mechvac Technologies Can Help
Rotary vane vacuum pumps offer reliable performance for various industrial applications, with easy maintenance and compact design.
However, selecting the right vacuum pump depends on your specific needs, including the required vacuum level, maintenance budget, and the type of material you’re handling.
At Mechvac Technology, we provide high-quality rotary vane vacuum pumps and guidance on selecting the right pump for your application.
Our team is dedicated to helping you achieve optimal performance, whether you’re in manufacturing, research, or any field requiring reliable vacuum technology. Let us support you with innovative solutions that ensure efficiency and long-term productivity.